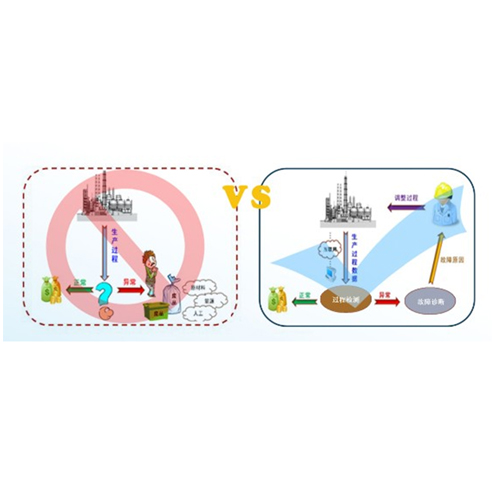
Currently, most injection quality control modes are predominantly inspection checks and result controls This system has yet to establish an accurate prevention system because work experience is needed when identifying defects in the injection process. Therefore, faults are not found and solved in time due to the fast worker turnover rate and a lack of work experience, reducing the quality of products.
The injection process monitoring and fault diagnosis system developed by our Research Institute is based on real-time analysis for machine parameters. The system sends an automatic alarm when an abnormality is detected, quickly identifies common faults so as to reduce the probability of occurrence of quality accidents, shortens the time to deal with the failure, and greatly reduce the rejection rate of products.